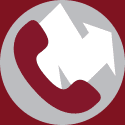
Call us!
To discuss your sortation system needs.
(704)525-1749
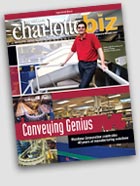
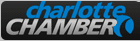
616 Pressley Road
Charlotte, NC 28217
ph (704) 525-1749
fax (704) 525-6129
Bronze/Silver/Gold Programs
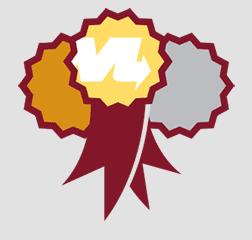
What is the BSG Program?
Well, it's not rocket science. In order to ensure consistent trouble-free operation of your Mantissa Material Handling System, a proactive approach needs to be taken, including a plan of action.
Our recommendation is that such a plan be comprised of two elements: The customer’s routine on-site maintenance efforts utilizing its own internal staff trained by Mantissa and periodic site inspections by Mantissa personnel under our Bronze/Silver/Gold Preventative Maintenance Program.
The Mantissa Bronze/Silver/Gold Program is an organized and cost-effective endeavor to enhance and support the established maintenance and service efforts of our customers. This program is designed with flexibility to meet the diverse needs and circumstances of our clients, including varying levels and expertise of maintenance staff, differing amounts of machine use, and unique business philosophies.
Bronze, Silver, and Gold represent the three levels of service available, based on the number of system inspections the customer chooses per year.
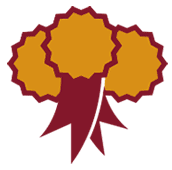
BRONZE
1 service call / year
Up to 3 man-days, includes complete electrical device and mechanical component review
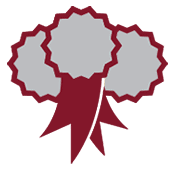
SILVER
2 service calls / year
Up to 3 man-days per trip, includes complete electrical device and mechanical component review
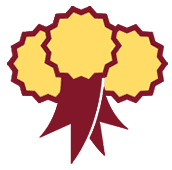
GOLD
3 service calls / year
Up to 3 man-days per trip, includes complete electrical device and mechanical component review
Bronze/Silver/Gold is no substitute for the required regular routine system maintenance as detailed in the Mantissa Operations and Maintenance Manuals. But, it does provide an enhanced effort by the experts who designed the equipment.
Note: The proposed number of hours per the various Bronze/Silver/Gold Program levels is not intended to suggest or imply in any way the total number of hours per year required for a sound preventative maintenance program.
Bronze/Silver/Gold does encourage the conscientious care of the equipment in terms of maintenance, training, and timely, effective communication. This program is the best course of action for our customers to protect their investment, and insure many years of productive, successful system operation.
How does it work?
The Mantissa Bronze/Silver/Gold Preventative Maintenance Program is proven valuable through the various program features that have evolved over the years to provide thorough, effective results.
Preventative Maintenance Procedure and Check List
The job site inspection is guided by a concise procedure and checklist. It includes a visual inspection and physical inspection of the sortation system components. This may be a full inspection (i.e. - drive systems) or a random inspection (i.e. - tilt modules) depending on the type of components. Regardless, there is sufficient inspection to form an expert opinion on the condition and maintenance of the system.
Correction of Site Conditions
Although the primary goal is a thorough inspection and assessment of the system condition, Mantissa will make adjustments or corrections as time and resources allow.
Office Inspection of Critical Components
In some cases, as part of our work on-site and with customer approval, Mantissa will remove and replace samples of the sorter core components (TipLoc™, tilt module and axle assemblies, etc.). The replacement parts are typically “borrowed” from the spare parts cart. The removed parts are sent to Mantissa’s headquarters for a more detailed and comprehensive inspection.
Return of Sample Inspection Components
Mantissa’s engineers inspect the sample components and provide feedback in the trip report. This input from additional resources adds further insight to the condition of the system. The sample parts are then returned to the customer in serviceable condition. Any parts or labor required to bring the sample components to serviceable condition is provided at no additional charge.
Off Hours Maintenance Work
Other than observation, most of the inspection and adjustments need to be done during hours when the sorter is not in use for production. Special arrangements may be necessary for access to the equipment during the “off” hours.
Trip Duration
In most cases the inspection and report takes two days on site.
Customer On Site Support
For security and safety reasons, our customers are required to provide at least one experienced maintenance staff personnel to assist Mantissa during the complete inspection process.
What areas of the system does the B/S/G Program cover?
The job site inspection encompasses the following areas of the sortation system:
![]() |
Linear Induction Drives (LID) or Green Drives | ![]() |
Tray Straighteners |
![]() |
Carrier Assemblies | ![]() |
Inch Pulse Array |
![]() |
Tilt Modules | ![]() |
Chute Systems |
![]() |
Trays | ![]() |
Automatic Inductors |
![]() |
TipLoc Assemblies | ![]() |
Safety Related Equipment |
![]() |
Additional Controls Equipment – Empty/full tray sensors, tip verify sensors, chute jam and chute full sensors, emergency stop switches, etc. | ![]() |
General Site Inspection – machine hours, maintenance log review, spare parts inventory, etc. |
What are the benefits of the B/S/G Program?
Mantissa Expertise
As the manufacturer, Mantissa is most capable of inspecting and analyzing the operation and performance of its systems and assessing the level of care. We come in as an objective outsider with both experience and an objective approach to evaluate the equipment and suggest maintenance improvements in support of the customer’s ongoing initiatives.
Program Customization
Mantissa varies the program to suit the unique levels of need of our various customers.
Supplemental Staff Training
Training occurs naturally, as Mantissa works along with the client's staff.
Detailed Report of Site and Office Review of System
Mantissa utilizes a Preventative Maintenance Procedure and Check List that includes observations and comments from both our field and office staff related to the condition and maintenance of the
system. This working document is reviewed and forwarded to our customers as a complete record of the trip. This report summarizes Mantissa’s actions, findings and recommendations, providing the customer with valuable feedback for establishing a more
effective or improved maintenance program.
How much does the B/S/G Program cost?
Pricing
Call our Mantissa Customer Service Department at 704-525-1749 or email us at CustomerService@MantissaCorporation.com for current rates.
Invoicing
Each level of service has a base price plus travel expenses. The base price is invoiced and paid at the time of enrollment or renewal. Invoicing for the trip related expenses is done after each trip is completed and the trip report is issued.
Expenses
Travel related expenses (hotels, airfare, rental car, and per diem) are invoiced at cost plus 10%.
Period of Contract
This is a one-year program. It starts at the time of enrollment, which may not coincide with the calendar year.
Scheduling
At the time of enrollment or renewal, Mantissa sets up tentative timeframes that are convenient for all parties. As the proposed time approaches, the actual trip dates are confirmed. Mantissa generally locks in the trip schedules early enough to take advantage of advance travel discounts. Pricing is based on Monday through Friday service days.
Cancellation
If circumstances arise that make it necessary for the client to postpone or cancel a trip scheduled for within (14) days, the client will be responsible for all costs resulting from altered or cancelled travel arrangements.
How do we sign up for the B/S/G Program?
Call Us!
We’ll be happy to discuss further details of the Mantissa Bronze/Silver/Gold Preventative Maintenance Program and help customize a program to meet your specific needs. Call our Mantissa Customer Service Department at 704-525-1749 or email us at CustomerService@MantissaCorporation.com for more information, and learn how you can add years of beneficial use to your Mantissa sortation system.
back to top